Betriebsdatenerfassung
Inhaltsverzeichnis
Definition
Unter dem Begriff Betriebsdatenerfassung (BDE) kann man ganz allgemein die Erfassung von Ist-Daten über Zustände und Prozesse in Betrieben verstehen. Betriebsdaten können entweder Maschinendaten und Prozessdaten sein. Betriebsdatenerfassung (BDE) ist die informationstechnische Grundlage für den Betrieb eines manufacturing execution system (MES) oder enterprise resource planning system (ERP)
Maschinendaten
Was sind Maschinendaten?
Im modernen Maschinenbau werden Maschinen durch Industriesteuerungen kontrolliert. Wie der Name bereits verrät, handelt es sich um Daten, die digital in Maschinen anfallen. Die reibungslose Kommunikation der Speicherprogrammierbaren Steuerung (SPS) mit den Sensoren der Maschine ist Voraussetzung für die Automation. Im Shopfloor (neudeutsch für Werkstatt oder Fertigung) einer Smartfactory wachsen Maschinen und Datenverarbeitungssysteme zu einem komplexen Cyber-pysischen-System (CPS) zusammen. Alle beschreibenden Daten innerhalb dieses Netzwerkes, die sich auf den Ist-Zustand der Produktionsanlage beziehen, können als Maschinendaten bezeichnet werden. In diesem Zusammenhang steht das Kürzel "MDE" für Maschinendatenerfassung
Warum baut man in Zukunft Smart Factorys?
Smart manufactoring ist das erklärte Ziel von Industrie 4.0. Durch Verschmelzung von Cyber-physischen-Systemen und intelligenter Vernetzung soll eine vollautomatisierte Produktion - von der Bestellung durch den Kunden bis zur Auslieferung - umgesetzt werden. Die Smart Factory ist in der Lage, für den Kunden vollkommen individualisierte Produkte ohne menschlichen Eingriff zu fertigen. Das Ermöglicht die Produktion von Einzelstücken zum Großserienpreis. Neben den Fertigungsanlagen sind auch die Logistiksyteme zum Betrieb der Fabrik selbstorganisierend. Das bedeutet, dass Maschinen autonom miteinander kommunizieren und innerhalb eines definierten Rahmens auch Entscheidungen treffen. Die technische Basis dafür bildet das Internet of Things (IOT) oder speziell das Industrial Internet of Things (IIOT). Die Steuerung des smart manufactoring ist ohne eine umfassende Betriebsdatenerfassung (BDE) ist nicht möglich
Was ist ein Cyber-physisches System?
Ein Cyber-physisches System, engl. „cyber-physical system“ (CPS), bezeichnet den Verbund informatischer, softwaretechnischer Komponenten mit mechanischen und elektronischen Teilen, die über eine Dateninfrastruktur, wie z. B. das Internet, kommunizieren. Ein cyber-physisches System ist durch seinen hohen Grad an Komplexität gekennzeichnet. Die Ausbildung von Cyber-physischen Systemen entsteht aus der Vernetzung eingebetteter Systeme durch drahtgebundene oder drahtlose Kommunikationsnetze.[1]
Beispiele
- Sensorendaten (Drehzahlen, Temperaturen)
- Aktorendaten (Betriebsbereitschaft, Position, Zustand)
- Verbräuche (Energie, Hilfsmittel, Material)
- Zählerstände (Betriebsstunden, gefertigte Stückzahlen)
- Störungsmeldungen (Normwertabweichung, Verschleiß)
- Unterbrechungsmeldungen (Standzeiten, Eingriff durch Bedienerpersonal)
Betriebsdatenerfassung Open Source: » Jetzt anfragen +49 365 855 038 25 oder per Email kontakt@archium.org
Anwendung
Maschinendatenerfassung (MDE) ist nicht nur wegen des Soll-Ist-Abgleichs innerhalb einer SPS für die Automation von enormer Bedeutung. Maschinendaten liefern auch wichtige Informationen zur Optimierung von Instandhaltungsroutinen. So lassen sich die Wartungsintervalle besser planen, wenn Verschleiß frühzeitig erkannt wird. Eine laufleistungsabhängige Wartung von Maschinen und Anlagen ist zwar weitgehend zuverlässig, schützt jedoch nicht vor ungeplantem Produktionsstillstand. Insbesondere bei Produktion großer Stückzahlen Just in Time[2] oder Just in Sequence[3] sind Stillstandskosten extrem hoch. Auch ein verschlissenes Werkzeug kann unbemerkt Ursache für Schlechtteile in der Produktion sein. Der vorzeitige Wechsel kostenintensiver Ersatzteile, unabhängig vom Grad der Abnutzung, ist ineffizient. Eine Lösung der Problematik verspricht vorausschauende Instandhaltung (Predictive Maintainance[4]). Selbstoptimierende Algorithmen ermitteln mit statistischen Methoden aufgrund einer Fülle von Betriebsdaten (Condition Monitoring[5]) den optimalen Wartungszeitpunkt einer Maschine, sodass Ersatzteilbestellungen ausgelöst werden können, noch bevor der Instandsetzungsfall eintritt. Das reduziert die anlagenbedingte Standzeit auf ein Minimum und bedeutet maximale Auslastung bei geringstmöglichen Wartungskosten.
Prozessdaten
Was sind Prozessdaten?
Im Gegenteil zu den Maschinendaten stammen Prozessdaten nicht von Anlagen bzw. Maschinen selbst, sondern beschreiben Parameter des Fertigungsprozesses, auf welchen die Maschine einwirkt. Die Prozesswerte werden mittels analoger und digitaler Sensoren gewonnen. In der Verfahrenstechnik ist Prozessdatenerfassung (PDE) die Grundlage für die Erkennung von Zusammenhängen in der Fertigung. Die anschließende datentechnische Auswertung liefert dem Qualitätsmanagement die notwendige Transparenz für eine kontinuierliche Prozessoptimierung und Dokumentation (Prozessdaten Reports). Das Erfassen, Auswerten und Visualisieren von Prozessdaten ist die informationstechnische Grundlage für die intelligente Produktionsplanung und Fertigungssteuerung(smart manufactoring).
Beispiele
- Qualitätsparameter (Fertigungstoleranzen, Oberflächengüte)
- Prozessparameter (Ist-Werte: Temperatur, Anpressdruck, Mengen)
- Maschinenkonfiguration (Soll-Werte: Temperatur, Anpressdruck)
Betriebsdatenerfassung Open Source: » Jetzt anfragen +49 365 855 038 25 oder per Email kontakt@archium.org
Anwendung
Prozessdaten werden nicht erst seit dem Aufkommen von Industrie 4.0 gesammelt. Die Erkenntnisse im Qualitätsmanagement waren schon jeher Grundlage für eine Justierung von Prozessen und Anlagen in der Produktion. Neu ist allerdings, dass die Optimierung der Produktionsprozesse bereits vor dem Durchlaufen der Qualitätskontrolle erfolgt. Die Überwachung und Auswertung von Prozesswerten in Echtzeit ermöglicht eine frühzeitige Fehlererkennung während der Fertigung eines Werkstückes. Machine Learning [6] nutzt statistische Methoden, um Fehlerbilder lange vor der Entstehung von Ausschuss zu erkennen. Dies kann einen justierenden Eingriff durch die automatisierte Fertigungssteuerung oder auch einen Produktionsstopp nach sich ziehen. Sich anbahnende Qualitätsmängel lassen sich so bereits im Produktionsprozess korrigieren. Die Anwendung von Predictive Maintainance[7] in der Fertigung optimiert den Verbrauch von Roh- und Hilfstoffen sowie Energie und Zeit.
Erfassung
Wie lassen sich Betriebsdaten erfassen?
In modernen Betrieben erfolgt die Betriebsdatenerfassung (BDE) durch ein Manufactoring Execution System (MES)[8]. Die auch als Produktionsleitsystem (PLS) bezeichnete Software ist über Schnittstellen direkt mit den Systemen der Prozessautomation in der Fertigung vernetzt. Durch die Datenerfassung in Echtzeit kann die Produktion mithilfe des MES kontrolliert und gesteuert werden. Die Module einer solchen Software zur Betriebsdatenerfassung (BDE) sind sehr umfangreich und flexibel, stoßen jedoch immer dann an ihre Grenzen, wenn eine Erfassung von bestimmten Betriebsdaten nicht möglich ist. Dies kann beispielsweise durch fehlende Schnittstellen der Fall sein.
Welche Schnittstellen sind üblich?
OPC
Ursprünglich stand das Akronym OPC für OLE for Process Control und war der Name für standardisierte Software-Schnittstellen, die den Datenaustausch zwischen Anwendungen unterschiedlichster Hersteller in der Automatisierungstechnik ermöglichen sollten. Durch die fortschreitende Weiterentwicklung dieser Schnittstellen und die damit einhergehende Abnahme der Relevanz des OLE-Objektsystems wurde der Standard im November 2011 in Open Platform Communications umbenannt. Deshalb wird heute zumeist die Bezeichnung OPC genutzt. Die aktuelle Spezifikation von OPC wird OPC Unified Architecture (OPC UA) genannt.[9]
OPC UA
OPC Unified Architecture (OPC UA) ist ein Standard für den Datenaustausch als plattformunabhängige, service-orientierte Architektur (SOA). Als neueste Generation aller Spezifikationen der Open Platform Communications (OPC) von der OPC Foundation unterscheidet sich OPC UA erheblich von ihren Vorgängerinnen insbesondere durch die Fähigkeit, Maschinendaten (Regelgrößen, Messwerte, Parameter usw.) nicht nur zu transportieren, sondern auch maschinenlesbar semantisch zu beschreiben.[10]
REST
Representational State Transfer (abgekürzt REST, seltener auch ReST) bezeichnet ein Programmierparadigma für verteilte Systeme, insbesondere für Webservices. REST ist eine Abstraktion der Struktur und des Verhaltens des World Wide Web. Der Zweck von REST liegt schwerpunktmäßig auf der Maschine-zu-Maschine-Kommunikation.[11]
MQTT
Das Message Queuing Telemetry Transport (MQTT) ist ein offenes Netzwerkprotokoll für Machine-to-Machine-Kommunikation (M2M), das die Übertragung von Telemetriedaten in Form von Nachrichten zwischen Geräten ermöglicht, trotz hoher Verzögerungen oder beschränkter Netzwerke.[12]
Auswertung
Die Analyse der gesammelten Daten
Das MES erfasst die Werte entweder direkt an der Schnittstelle der Maschinensteuerung oder von steuerungsunabhängiger Sensorik, wie sie im Retrofitting von Altmaschinen eingesetzt wird. Alle Daten werden kontinuierlich über ein industrielles Netzwerk in der Produktion, zum Beispiel ProfiNet (PN), zum MES-Server übertragen. Mit einem Datenlogger, wie dem archium® »hoplite« können zusätzliche Daten erfasst, aufbereitet und übergeben werden. Manche Systeme erfordern eine aufwendige Schnittstellenprogrammierung oder teure Zusatzmodule für die Integration.
Auch ohne ein komplexes Produktionsleitsystem kann die gezielte Erfassung und Auswertung von Prozessdaten sinnvoll sein. Für das Auslesen von Steuerungen hat archium® einen Industrie-PC mit Open-Source-Komponenten für LINUX Betriebssysteme entwickelt. Nach dem Auslesen der Werte erfolgt die Weiterverarbeitung direkt im Schaltschrank der Maschine.
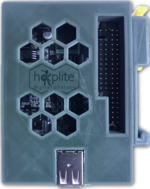
Der archium® »hoplite« 2025 ist ein UNIX basierter Industrie PC mit 4-Kernprozessor und der Möglichkeit zur Hutschienenmontage in einem Schaltschrank. Maschinendatenerfassung (MDE) wird damit direkt am Ort der Entstehung (z.B. in der Siemens S7 SPS oder dem OPC-Server) möglich, ohne das Netzwerk unnötig mit Traffic zu belasten. Die Kombination von Hard- und Software ist wie ein universelles Werkzeug einsetzbar:
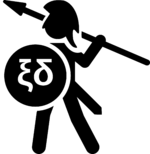
- INGEST (Daten lesen)
- PROCESS (Daten verarbeiten)
- EMIT (Informationen softwareunabhängig wiedergeben)
archium® entwickelt individuelle, maschinennahe Software, die automatische Analysen und flexible Auswertungen ermöglicht. Durch den Einsatz von Mehrkernprozessoren und der Programmiersprache „GO“ werden diese Prozesse nebenläufig ausgeführt. Das steigert die Verarbeitungsgeschwindigkeit und sorgt gleichzeitig für mehr Prozessstabilität beim Auslesen und Auswerten von Daten aus einer Steuerung (SPS).
Anwendungsmöglichkeiten
- Betriebsdatenerfassung (BDE)
- Maschinendatenerfassung (MDE)
- Prozessdatenerfassung (PDE)
- Zeiterfassung von Prozesszeiten
- Auswertungen von Ist-Daten und Soll-Daten im Vergleich
- Datenanalyse in Echtzeit
- SPS Datenbankanbindung
- Integration von SQL Datenbanken wie PostgreSQL und MySQL
- Datenaustausch mit beliebigen ERP Systemen, auch SAP
- Prozessdaten Reports - aus der SPS direkt in PDF
- Datensicherung von Netzwerkteilnehmern
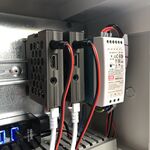
Mit der archium® »Digital Phalanx«, einem Verbund aus archium® »hoplites«, lässt sich das System bei größeren Datenströmen problemlos skalieren, ohne auf eine externe Cloudanwendung zurückgreifen zu müssen.
Die archium® »Digital Phalanx« 2025 ist ein UNIX-Hardwarecluster für Microservices im Anlagenbau. Mit dieser Open Source Software lässt sich eine Vielzahl von archium® »hoplites« in einem Netzwerk zu einer »Digital Phalanx« zusammenfassen.
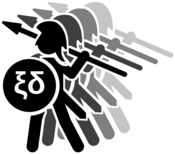
Unser Datenlogger sammelt Produktionsdaten in Echtzeit und stellt diese für eine Prozessdatenanalyse in der integrierten SQL-Datenbank für eine weitere automatisierte Verarbeitung zur Verfügung. Das Verarbeiten der Daten direkt am Ort ihrer Entstehung (am PC oder an der Industriesteuerung) senkt die Netzwerklast und macht unabhängig von Internet und Cloud.
Betriebsdatenerfassung Open Source: » Jetzt anfragen +49 365 855 038 25 oder per Mail: kontakt@archium.org
Visualisierung
Prozessdaten Reports
archium® liest kontinuierlich Prozessdaten aus Industriesteuerungen Ihres Produktionsnetzwerks und erstellt revisionssichere Reports zur Erfüllung von individuellen Nachweispflichten gegenüber Behörden und Kunden. Die Prozessdatenerfassung erfolgt mit einem archium® hoplite direkt und nebenläufig im Schaltschrank, ohne das Produktionsnetzwerk durch vermeidbaren TCP/IP-Datenverkehr zu belasten. Die Reporterstellung ist unabhängig von einem vorhandenen MES oder PPS. Die Prozessdatenreports im PDF-Format können in der integrierten Open Source Datenbank bequem abgelegt und verwaltet werden.
Browser Visualisierung und Web Apps
Die Visualisierung der Live-Daten aus der Prozessdatenerfassung setzen wir im Browser um. »WebAssembly (WASM)« ist ein moderner Bytecodestandard, welcher in einer low level virtual machine (LLVM)[13] große Datenströme leichter verarbeiten und damit schneller visualisieren kann. Aus unserer Sicht ist WASM ist das perfekte Werkzeug zur Umsetzung von WebApps mit einer agilen Anzeige und Bedienung.
![[14] [14]](/images/d/da/HCoutput5.png)
Sicherung
automatische Sicherung mit Ektypus Backup
Das Wort »Ektpus« stammt aus dem Griechischen und bedeutet »Nachbildung«, »Abbild« oder »Kopie«. Beim »Ektypus-Automation-Backup« handelt es sich um eine Software, die automatisch Dateien oder Verzeichnisse archiviert. Eine permanente Datenerfassung erfordert gleichzeitig eine zuverlässige Datensicherung. Das archium® »Ektypus-Automation-Backup« sichert automatisiert Ihre Betriebsdaten und Verzeichnisse und legt diese in einem Archivfile ab. Der Archivierungsprozess ist so angelegt, dass individuell definierbare Altersstufen desselben Archivs verfügbar bleiben.
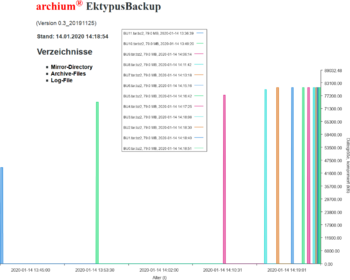
Damit lassen sich auch bereits gelöschte Inhalte von archivierten Verzeichnissen bequem wiederherstellen. Um den Anforderungen der DSG-VO gerecht zu werden, können zu löschende Dateien markiert und in einem gesonderten Prozess in allen kompromittierten Backupständen entfernt werden.
Die Software ist auf jedem aktuellen UNIX-Derivat lauffähig. Somit bleibt das Archiv unabhängig von proprietärer Software wie Windows oder Apple. Der Sicherungsprozess erfolgt nebenläufig in Zeiten geringer Netzwerklast. Damit beeinträchtigt das »Ektypus-Automation-Backup« Ihren Produktivprozess nicht.
Das Besondere:
- Sicherung von außerhalb des zu sichernden Systems
- Sicherung aus täglich unterschiedlichen Adressbereichen
- Nach Backupende automatische Schließung der Ports
- Inhaltsverzeichnis als Textfile für jedes Archiv
- Archivfiles sind nach Entpacken einfach lesbar
- komplexe Backupszenarien frei programmierbar
Anwendungsmöglichkeiten:
- automatische Datensicherung von Cloudanwendungen über API
- automatische Datensicherung von Windows PCs
- automatische Datensicherung von Netzwerkservern
- automatische Datensicherung von Datenbanken
- automatische Datensicherung von sonstigen Komponenten in industriellen Netzwerken (z.B. Siemens S7)
Viele Firmen nutzen täglich Cloudanwendungen wie Finanzsoftware, Software zur Produktionsplanung, Zeiterfassung oder zur Kommunikation mit dem Kunden. archium® mit eingeschlossen. Es scheint einfach, sicher und vor allem bequem. Die Software ist immer aktuell, beansprucht kaum Hardwareressourcen oder Administration im Betrieb, der Speicherplatz scheint unbegrenzt und die Abrechnung erfolgt lizenzgenau. Was spricht also dagegen? Immerhin werden über diese Anwendungen hochsensible, geschäftskritische Daten erfasst und außerhalb des eigenen Einflussbereiches gespeichert. Zunächst erstmal gar nichts. Bei genauerer Betrachtung besteht allerdings ein sehr starkes Abhängigkeitsverhältnis:
- vom Internetzugang des Anwenders
- vom Internetzugang des Anbieters
- von einer Schnittstelle, über die alle Daten ausgetauscht werden
- von zwischengeschalteten Zahlungsdienstleistern
- vom Anbieter selbst (technisch und im Falle einer Insolvenz)
Laufen diese Anwendungen jahrelang ohne Störung, ist ein beachtlicher Teil an elementaren Geschäftsdaten bereits in der Treuhand des Cloudanbieters. Ist der Server des Dienstleisters plötzlich nicht erreichbar, spüren Sie sofort, was dies für weitreichende Konsequenzen haben wird!
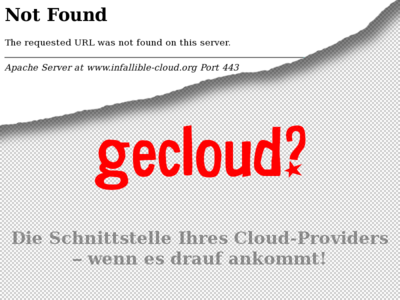
Mit dem »Ektypus-Automation-Backup« von archium® sichern Sie Ihre Daten aus der Cloud kontinuierlich automatisiert lokal über die API-Schnittstelle Ihres Clouddienstanbieters.
Ektypus-Automation-Backup plus
plus archium® hoplite
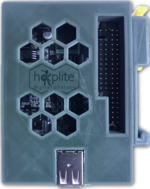
Um das Backupsystem in jedem beliebigen Netzwerk integrieren zu können, wird die Software gleich mit einem einsatzbereiten Einplatinencomputer (»Hoplite«) samt Betriebssystem ausgeliefert. Die Erfassung und Verarbeitung der Daten erfolgt nebenläufig und blockiert somit keine vorhandenen Hardwareresourcen.
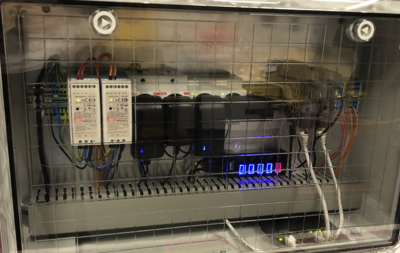
archium® hoplite plus Schaltschrank
In einem Schaltschrank (IP65) samt Hard- und Software verpackt, findet das »Ektypus-Automation-Backup« seine Anwendung im klassischen Büro oder in industrieller Produktionsumgebung. Die Hardwareausstattung wird individuell auf die Anforderung des Kundennetzwerks zugeschnitten.
Wir verwenden hier bewusst eine Analogie zu den Spartanern Griechenlands, welche im 5. Jahrhundert (vor unserer Zeitrechnung) aus Kriegern (Hopliten) einen überlegenen Kampfverband (Phalanx) formten und damit überragende Erfolge im Feld erzielten. Sie hatten der persischen Übermacht widerstanden, später hatte der Große Alexander mit Ihnen ein Weltreich besiegt und errichtet, und selbst der junge Sokrates hatte einst als Hoplit gekämpft.
Der Hoplit steht für uns synonym für die starke Einzelkomponente, die im Verbund ihre Kraft potentiert.
- ↑ https://de.wikipedia.org/wiki/Cyber-physisches_System
- ↑ https://de.wikipedia.org/wiki/Just-in-time-Produktion
- ↑ https://de.wikipedia.org/wiki/Just-in-sequence-Produktion
- ↑ https://de.wikipedia.org/wiki/Prädiktive_Instandhaltung
- ↑ https://de.wikipedia.org/wiki/Condition-Monitoring
- ↑ https://de.wikipedia.org/wiki/Maschinelles_Lernen
- ↑ https://de.wikipedia.org/wiki/Prädiktive_Instandhaltung
- ↑ https://de.wikipedia.org/wiki/Manufacturing_Execution_System
- ↑ https://de.wikipedia.org/wiki/Open_Platform_Communications
- ↑ https://de.wikipedia.org/wiki/OPC_Unified_Architecture
- ↑ https://de.wikipedia.org/wiki/Representational_State_Transfer
- ↑ https://de.wikipedia.org/wiki/MQTT
- ↑ [https://de.wikipedia.org/wiki/LLVM]
- ↑ https://prosys-weida.de Testversion einer Industrievisualisierung für die Firma Prosys